Phased Array
O que é Phased Array?
Atualmente a avaliação de defeitos e descontinuidades na indústria exigem dados cada vez mais precisos em relação à sua localização, forma e tamanho. A tecnologia de ultrassom Phased Array, pode fornecer dados de defeitos com precisão e exatidão para o padrões de aceitação baseados em normas e critérios de aceitação.
O Phased Array ou PAUT é uma extensão do ultrassom convencional e tem a habilidade de controlar e modificar eletronicamente as caraterísticas do feixe sônico de um transdutor/ cabeçote. Um transdutor Phased Array é composto de múltiplos pequenos cristais ultrassônicos, cada um dos quais pode ser pulsado individualmente. Ao variar o tempo do pulso de cada cristal individual, o feixe ultrassônico pode ser “direcionado” para um ângulo específico e distância focal – isto é, o feixe pode ser varrido através do objeto examinado. Essa habilidade permite que haja um considerável aumento na detecção de descontinuidades e maior precisão da sua localização.
O Phased Array é usado para detectar defeitos que não podem ser facilmente encontradas com métodos convencionais de ensaios não destrutivos, como radiografia e ultrassom manual / convencional. A VENTURA NDT é especializada no uso de Phased Array na indústria de petróleo e gás, naval, químico, petroquímico, metalúrgico, siderúrgico, mineração, aeroespacial, celulose e eólico. Especialmente para a construção de novas tubulações, oleodutos, vasos e componentes estruturais soldados fornecendo garantia de qualidade total. Também usamos a técnica em refinarias e usinas petroquímicas, quando inspeções rápidas e precisas são necessárias devido a restrições de tempo durante as paradas.
A tecnologia Phased Array é um método avançado de teste ultrassônico que pode ser usada para várias aplicações de inspeções diferentes.
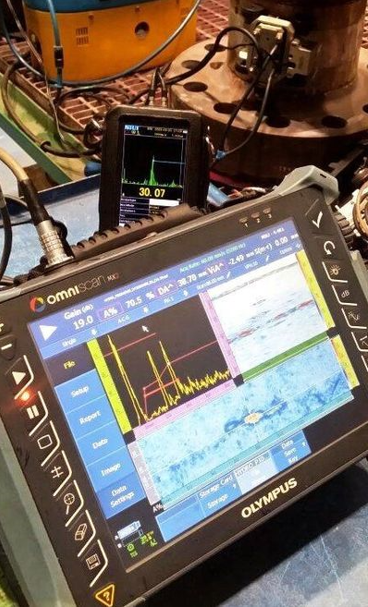
Inspeção Phased Array com Water wedge Hydroform em uma solda de inconel
Atualmente a avaliação de defeitos e descontinuidades na indústria exigem dados cada vez mais precisos em relação à sua localização, forma e tamanho. A tecnologia de ultrassom Phased Array, pode fornecer dados de defeitos com precisão e exatidão para o padrões de aceitação baseados em normas e critérios de aceitação.
O Phased Array ou PAUT é uma extensão do ultrassom convencional e tem a habilidade de controlar e modificar eletronicamente as caraterísticas do feixe sônico de um transdutor/ cabeçote. Um transdutor Phased Array é composto de múltiplos pequenos cristais ultrassônicos, cada um dos quais pode ser pulsado individualmente. Ao variar o tempo do pulso de cada cristal individual, o feixe ultrassônico pode ser “direcionado” para um ângulo específico e distância focal – isto é, o feixe pode ser varrido através do objeto examinado. Essa habilidade permite que haja um considerável aumento na detecção de descontinuidades e maior precisão da sua localização.
O Phased Array é usado para detectar defeitos que não podem ser facilmente encontradas com métodos convencionais de ensaios não destrutivos, como radiografia e ultrassom manual / convencional. A VENTURA NDT é especializada no uso de Phased Array na indústria de petróleo e gás, naval, químico, petroquímico, metalúrgico, siderúrgico, mineração, aeroespacial, celulose e eólico. Especialmente para a construção de novas tubulações, oleodutos, vasos e componentes estruturais soldados fornecendo garantia de qualidade total. Também usamos a técnica em refinarias e usinas petroquímicas, quando inspeções rápidas e precisas são necessárias devido a restrições de tempo durante as paradas.
A tecnologia Phased Array é um método avançado de teste ultrassônico que pode ser usada para várias aplicações de inspeções diferentes.
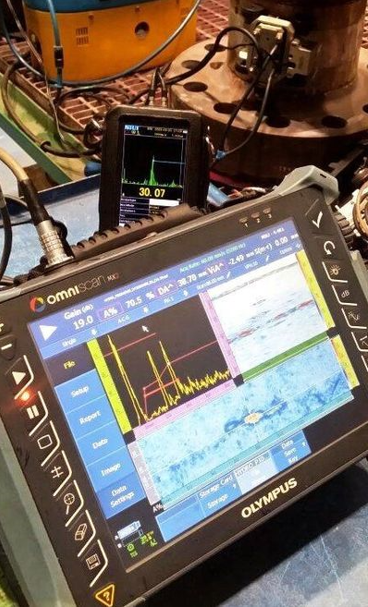
Inspeção Phased Array com Water wedge Hydroform em uma solda de inconel
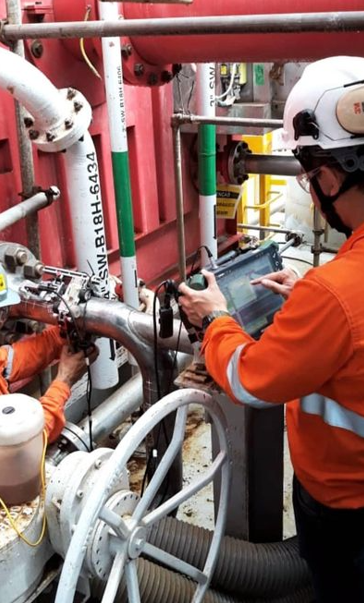
Aplicações do Phased Array
- Inspeção em Soldas de diversos diâmetros e geometrias
- inspeção em uma vasta gama de materiais. Ex.: Aço Inoxidável austenítico, Duplex, Super Duplex, Inconel, Incoloy, forjados, fundidos e etc…
- Mapeamento de corrosão
- Inspeção componentes de geometria altamente complexas . Ex.: Raízes da lâmina da turbina
- Tubulações de baixo diâmetro. Ex.: 1 3/4″, 1″.
Vantagens
Aumento na confiabilidade de inspeção, com redução da subjetividade da inspeção com ultrassom manual.
Maior precisão na detectabilidade de defeitos, possibilitando um índice de reprovação menor.
Redução dos tempos de inspeção. O Phased Array é no mínimo 2 vezes mais rápido do que o ultrassom manual.
- Capacidade de direcionar o feixe sem mover o transdutor, o que possibilita a inspeção de componentes onde o espaço seja reduzido e não haja acesso para varredura mecânica;
- Inspeciona soldas com vários ângulos a partir de uma única varredura, o que aumenta consideravelmente a probabilidade de detecção de descontinuidades.
- A possibilidade de focalização do feixe melhora a capacidade de dimensionamento de defeitos volumétricos.
- Laudos mais precisos e melhor controle de qualidade das soldas possibilitam o dimensionamento da profundidade e do comprimento de descontinuidades.
- Maior facilidade de rastreamento e auditoria dos serviços em razão do registro automático de 100% de toda a extensão da solda inspecionada. Os relatórios são customizados e podem ser impressos e/ou eletrônicos de acordo com a necessidade do cliente
Aplicações do Phased Array
- Inspeção em Soldas de diversos diâmetros e geometrias
- inspeção em uma vasta gama de materiais. Ex.: Aço Inoxidável austenítico, Duplex, Super Duplex, Inconel, Incoloy, forjados, fundidos e etc…
- Mapeamento de corrosão
- Inspeção componentes de geometria altamente complexas . Ex.: Raízes da lâmina da turbina
- Tubulações de baixo diâmetro. Ex.: 1 3/4″, 1″.
Vantagens
Aumento na confiabilidade de inspeção, com redução da subjetividade da inspeção com ultrassom manual.
Maior precisão na detectabilidade de defeitos, possibilitando um índice de reprovação menor.
Redução dos tempos de inspeção. O Phased Array é no mínimo 2 vezes mais rápido do que o ultrassom manual.
- Capacidade de direcionar o feixe sem mover o transdutor, o que possibilita a inspeção de componentes onde o espaço seja reduzido e não haja acesso para varredura mecânica;
- Inspeciona soldas com vários ângulos a partir de uma única varredura, o que aumenta consideravelmente a probabilidade de detecção de descontinuidades.
- A possibilidade de focalização do feixe melhora a capacidade de dimensionamento de defeitos volumétricos.
- Laudos mais precisos e melhor controle de qualidade das soldas possibilitam o dimensionamento da profundidade e do comprimento de descontinuidades.
- Maior facilidade de rastreamento e auditoria dos serviços em razão do registro automático de 100% de toda a extensão da solda inspecionada. Os relatórios são customizados e podem ser impressos e/ou eletrônicos de acordo com a necessidade do cliente
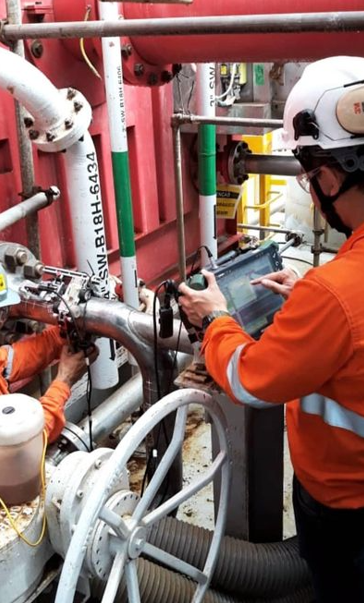
Phased Array e Radiografia
Na avaliação de ensaios não destrutivos (END), vários códigos permitem aos inspetores substituírem um método de inspeção por outro, desde que determinados requisitos sejam atendidos. Além disso, métodos de inspeção não baseada em códigos são constantemente revisados para melhorar o processo e reduzir os custos. Os métodos por ultrassom tornaram-se um substituto popular e aceito em inspeções que anteriormente empregavam métodos radiográficos.
Introdução
A radiografia e o ultrassom são técnicas de ensaios não destrutivos complementares. As duas podem realizar inspeções volumétricas de soldas e de componentes para defeitos como trincas, falta de fusão, porosidade, etc. A escolha entre uma e outra depende das decisões do processo externo ou de pequenas diferenças na capacidade de detecção de um teste específico. No entanto, o ultrassom começou a substituir a radiografia devido à sua praticidade e por estar em conformidade com os códigos da Sociedade dos Engenheiros Mecânicos dos Estados Unidos (ASME) e do Instituto Americano de Petróleo (API). Embora a maioria dos códigos não especifiquem o método ultrassônico, o ultrassom Phased Array (PA), particularmente, tem-se tornado o método mais popular nos processos de inspeção. O Phased Array também é utilizado juntamente com o método de tempo de voo da onda difratada (ToFD) quando inspetores usam unidades de aquisição e escâneres que podem usar os dois métodos simultaneamente. Antigamente, os processos de inspeção baseados em código geralmente seguiam o código do caso ou os anexos. No entanto, depois do aumento da utilização e da aceitação da indústria, os processos de inspeção ultrassônicos têm sido incorporados diretamente pelos principais códigos como, por exemplo, a ASME Sec. V. Art. 4, a partir de 2010. O equipamento de ultrassom Phased Array está a cada dia mais acessível, portátil e fácil de usar, tornando o ultrassom prático e um substituto seguro à radiografia.
Principais vantagens do ultrassom (em relação à radiografia):
Maior probabilidade de detecção (POD, sigla em inglês), especialmente para trincas e falta de fusão:
Na maioria das pesquisas realizadas, o ultrassom tende a detectar melhor os defeitos planares que a radiografia.
A dimensão precisa da altura do defeito, a menor rejeição ou reparo usam a Avaliação Crítica de Engenharia:
O ultrassom permite a medição da altura do defeito, o que permite a consideração volumétrica da gravidade do defeito (em vez de indicar apenas o tipo e o tamanho do defeito).
Ele não emite radiação, é seguro e não exige licença adicional ou pessoal.
Não precisa ser operado em áreas protegidas. Pode-se trabalhar normalmente quando se realizam testes ultrassônicos nas proximidades.
Não produz nenhum resíduo químico ou causa desperdício de material (diferentemente do filme utilizado na radiografia).
A análise ultrassônica em tempo real das soldas pode fornecer avaliação instantânea e respostas ao soldador.
A configuração e os relatórios de inspeção são em formato eletrônico (diferentemente do filme de radiografia).
Exemplos de códigos com a substituição da radiografia pelo ultrassom:
Código ASME Caso 2235
Código ASME Caso 179
Código ASME Caso 168
Código ASME Caso N-659
Código ASME N-713
API 620/650 App. U
ASME Sec. V Anexos exigidos
Equipamentos típicos de ultrassom e inspeções exigidas
Unidade de aquisição com retenção de dados em série e recurso de codificação de posição (por exemplo, o detector de defeitos OmniScan® ou o FOCUS PX™).
Um plano de rastreamento e o procedimento que documenta a estratégia de inspeção e os principais parâmetros (por exemplo, parâmetros configurados usando o software NDT SetupBuilder ).
Um escâner industrial (com codificador de posição) que pode rastrear repetidamente uma solda ou um componente (semiautomático ou automático).
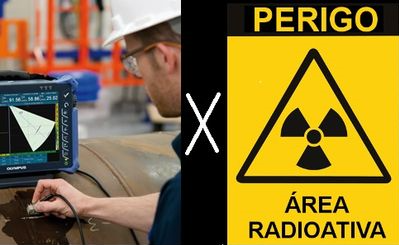